DESAFIOS E TENDÊNCIAS NA APLICAÇÃO DE SISTEMAS APS NO BRASIL
Uma abordagem empresarial e prática para a implementação de ferramentas avançadas de planejamento e programação da produção com menores riscos e resultados mais expressivos.
A implantação de ferramentas APS (Advanced Planning and Scheduling) já não é mais privilégio de algumas poucas grandes empresas. São cada vez maiores os relatos de projetos em empresas dos mais variados portes e segmentos e também são cada vez mais frequentes os casos de sucesso nos quais se obtém resultados expressivos com esta tecnologia. Porém, como toda tecnologia que causa grandes mudanças, diversos obstáculos surgem neste processo. Nessa linha, o presente artigo abordará alguns desafios encontrados e aspectos relevantes que devem ser considerados no momento de implantação do APS. Além de fazer uma revisão conceitual do tema, o texto tratará ainda de tendências futuras de aplicações da ferramenta.
Tradicionalmente a informatização da gestão da manufatura costuma ser deixada em segundo plano em grande parte das empresas. É quase uma regra dos fornecedores de Sistemas Integrados de Gestão (ERP) e integradores de sistemas iniciarem as implantações dos pacotes de ERP pelas áreas financeiras, contábeis e administrativas. Somente na fase final, após longos meses de projeto, são iniciadas as parametrizações dos módulos de manufatura, tais como o Planejamento das Necessidades de Materiais (MRP), o Planejamento de Capacidade (CRP) e o Plano Mestre de Produção (MPS).
Nesse momento, para aquelas empresas que obtêm sucesso e finalizam de forma satisfatória a implantação dos módulos industriais, começam a surgir questionamentos sobre a real aplicabilidade e a aderência destas ferramentas em relação aos seus processos produtivos. Esta situação é justificada pelo fato dos módulos de manufatura existentes nos sistemas de ERP não contemplarem uma série de necessidades específicas das atividades de Planejamento, Programação e Controle da Produção (PPCP). Esta frustração é agravada ao passo que as atividades de PPCP exercem elevados impactos na competitividade das empresas, tendo em vista que o seu desempenho tem influência direta nos níveis de estoques de produtos acabados, no material em processo, na confiabilidade, na performance de entrega, na flexibilidade, na capacidade aparente de produção, dentre outros fatores.
Dentre estas atividades, certamente as de programação da produção (plano de curto prazo) são as mais carentes em nível de sistema. Tais tarefas, a princípio, deveriam ser simples, pois estariam sendo suportadas por um plano de produção de longo prazo e por um plano mestre de médio prazo, com as necessidades de capacidade de produção analisadas e equacionadas em tempo hábil. Porém, dentro da dinâmica empresarial, instabilidades de curto prazo, como cancelamentos, adiantamentos ou acréscimos em pedidos dos clientes, alterações nas especificações dos itens, ou ainda, deficiências na qualidade e nos ritmos de trabalho, fazem com que a eficiência do sistema produtivo dependa fundamentalmente de um processo dinâmico de sequenciamento e emissão do programa de produção (TUBINO, 2007).
Conhecendo a importância estratégica que as atividades de PPCP exercem em uma organização, as indústrias vêm preocupando-se cada vez mais com estes temas. Segundo Zattar (2004), pesquisas na área começaram em meados do século XX. Na década de 1970 os computadores tornaram-se mais poderosos e baratos, viabilizando o surgimento dos softwares como os sistemas de MRP. Como os MRPs eram limitados e não tratavam da capacidade dos recursos produtivos da empresa em nenhum nível de sua solução, na década de 1980 foram lançados os sistemas de Planejamento de Recursos de Manufatura (MRP II).
Assim como o MRP, que não considerava os recursos produtivos, o MRP II também possuía uma deficiência: considerava como infinita a capacidade dos recursos instalados e como constantes os lead times, de forma independente da demanda. Esta falta de visibilidade dos recursos resultava em um plano de produção não confiável e somente referencial. Em paralelo aos sistemas MRP II, outra solução começava a ser pesquisada, os Sistemas de Programação com Capacidade Finita (FCS – Finite Capacity Scheduling) e posteriormente os Sistemas de Planejamento e Programação Avançados (APS Advanced Planning and Scheduling) (ZATTAR, 2004).
Portanto, os sistemas APS foram desenvolvidos para suprir importantes lacunas do gerenciamento de produção das indústrias. Desde a sua criação, diversos sistemas foram desenvolvidos no mundo todo e, atualmente, o mercado de softwares APS pode ser dividido em três principais grupos de fornecedores:
a) fornecedores de ERP que possuem um módulo de APS como parte integrante da sua plataforma;
b) fornecedores de uma plataforma completa de Supply Chain Management que possuem um módulo de APS como parte integrante do seu pacote de soluções;
c) fornecedores independentes e especialistas em softwares APS.
Ao longo dos últimos anos, as ferramentas APS foram passando por um processo de amadurecimento, no qual tanto as indústrias quanto os fornecedores dos sistemas passaram a compreender, de forma mais abrangente, as barreiras e desafios encontrados nas implantações. Assim como toda nova tecnologia, os softwares APS causam impactos culturais e demandam mudanças comportamentais nas empresas. Entretanto, as pesquisas têm mostrado que os benefícios dos APS são bastante expressivos e geralmente estão relacionados a: redução dos estoques, melhor aproveitamento dos recursos, redução dos atrasos nas entregas e redução dos materiais em processo.
Na estreita do amadurecimento do conceito do APS, as empresas passaram a buscar novas ferramentas que trouxessem uma maior aproximação com os elos da sua cadeia. Como já estava consolidada uma sistematização das áreas administrativas e de manufatura, a partir deste século as organizações passaram a enxergar a necessidade de atuar de forma colaborativa ao longo da cadeia de suprimentos, buscando a satisfação dos clientes finais e a eficiência de todos os elos da cadeia.
Foi nesse momento que se verificou o lançamento de uma nova onda de implantação de pacotes de tecnologia da informação: a dos sistemas de Supply
Chain Management. Estes sistemas ofereciam módulos como Planejamento dos Transportes (TMS), Gerenciamento de Armazéns (WMS) e Planejamento de Demanda.
O artigo está focado em um estudo sobre as ferramentas APS baseando-se em materiais de pesquisa, em bibliografias acadêmicas e na experiência profissional dos autores. Inicialmente será feita uma breve revisão teórica para contextualizar o assunto. Em seguida, serão discutidos os principais desafios e aspectos relevantes que devem ser considerados para a condução de uma implantação de APS. Por fim, o artigo propõe uma análise sobre tendências futuras de aplicações da ferramenta.
Sistemas APS
Os softwares APS são ferramentas especialistas em planejamento e programação avançada de operações. Estes sistemas utilizam o conceito de programação com capacidade finita e são capazes de considerar diversas variáveis de um sistema produtivo necessárias para gerar um plano de produção viável e factível.
Os sistemas APS não foram desenvolvidos com o intuito de substituir nem de excluir os sistemas MRP e MRPII, mas sim de suprir as suas carências e de complementá-los. Ou seja, apesar de estarem aptos a trabalhar de forma isolada (standalone), os sistemas APS surgiram com o propósito de funcionar integrados com outros softwares, como forma de evitar a duplicidade de dados cadastrais e a sobreposição conflitante com os demais sistemas de gestão (FAÉ; ERHART, 2005; ERHART et al, 2007). De acordo com a abordagem de Ritzman & Krajewski (2004), o MRP transfere ao APS a informação detalhada da demanda que deve ser programada e esse devolve ao MRP as datas realistas de início e fim de produção das operações, para fins de reprogramação das necessidades de materiais. Segundo Corrêa et al, (2001), este modelo de aplicação é classificado como um sistema híbrido, tendendo a ser bastante utilizado, pois atua de forma complementar e preenche as carências tradicionais de um sistema de PPCP. Este modelo pode ainda ser descrito em três níveis hierárquicos da manufatura: longo (por exemplo, MPS), médio (por exemplo, MRP) e curto prazo (por exemplo, APS) (VOLMANN et al, 1997).
Um exemplo hipotético de um sistema híbrido MRP/APS/MES de planejamento, programação e controle da produção pode ser observado na figura abaixo. Neste modelo, o MRP gera as ordens de produção e o APS realiza a programação fina da produção, disponibilizando as informações de execução para a fábrica em formato eletrônico através de um sistema MES (Manufacturing Execution System). A seguir, as datas realistas de início e fim das ordens são retornadas para o ERP para que sejam revisadas as datas de planejamento de aquisição de materiais. À medida que a programação é realizada na fábrica, os apontamentos de paradas de máquina e andamento das operações são coletados através do sistema MÊS e enviados para o APS, para que a programação possa ser corrigida e atualizada novamente.
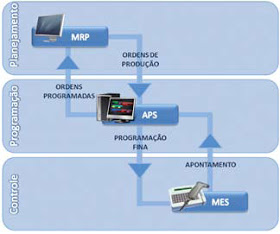 |
Modelo hipotético de um sistema de PPCP com integração entre MRP, APS e MES |
Devido ao nível de detalhe que pode ser absorvido na modelagem do sistema produtivo, os softwares APS são bastante adequados para empresas que atuam em ambientes complexos e dinâmicos, pois conseguem absorver e refletir a maioria das variáveis envolvidas nas decisões sobre a programação. Os sistemas APS podem ser empregados em praticamente todos os tipos de sistemas produtivos, mas seus benefícios são sensivelmente maiores nos ambientes que contêm os seguintes elementos (CARVALHO, 2009):
Ø a programação de produção é preponderantemente limitada pela capacidade e não pela disponibilidade dos materiais;
Ø a estrutura de produtos contempla montagens e as operações possuem características que necessitam de sincronismo;
Ø o tamanho dos lotes e o sequenciamento das ordens de produção interferem nas perdas por setup e influência na produtividade;
Ø a demanda não é conhecida e varia significativamente ao longo do tempo;
Ø a variação do mix da demanda altera dinamicamente os gargalos da produção;
Ø o lead time é muito variável em função da carga da fábrica;
Ø os fluxos de produção são complexos e difíceis de serem tratados através de gestão visual.
Dentre os principais resultados verificados nas implantações, destacam-se:
Ø melhoria no nível de serviço;
Ø redução do material em processo;
Ø aumento de capacidade aparente;
Ø redução de custos de estoques;
Ø redução de custos de mão-de-obra e terceirização.
Principais desafios e aspectos relevantes para implantação
Apesar de ser uma das ferramentas mais solicitadas pelas gerencias industriais da maioria das empresas, é preciso reconhecer que um projeto de implantação de ferramenta APS envolve uma série de desafios para que possa tornar efetivo todo o seu potencial de geração de resultado. A seguir, são destacados os principais desafios e aspectos relevantes que as empresas precisam considerar para obter sucesso na seleção e implantação de um sistema APS.
Identificar os requisitos-chave
Antes de selecionar uma solução APS, é fundamental identificar com todas as áreas envolvidas quais são os principais objetivos que devem ser traçados e, a seguir, quais os requisitos-chave que devem ser considerados. Ao longo do processo de seleção, funcionalidades adicionais e objetivos secundários podem desviar o foco de atenção. Os esforços devem estar concentrados na obtenção de um rápido retorno sobre o investimento realizado, através de uma solução simples de ser implantada e ao mesmo tempo focada nos principais objetivos.
Neste sentido, é importante verificar que a incorporação de funcionalidades sofisticadas e que não são fundamentais para o bom desempenho da solução podem ser agregadas em etapas posteriores ao início da utilização do sistema. A definição clara e homogênea das expectativas de todas as áreas e a relação dos requisitos necessários são os principais fatores que devem ser considerados para minimizar o risco de frustração entre as partes interessadas.
Selecionar software e fornecedor qualificado
A escolha do fornecedor de software APS mais adequado passa necessariamente por um processo de seleção em que diversos critérios devem ser considerados. Para cada empresa, estes critérios poderão ter pesos diferentes e ter mais ou menos importância durante o processo. Dado o sensível crescimento no volume de implantações, autores como Pacheco e Cândido (2002) vêm desenvolvendo estudos para determinar uma metodologia para seleção de soluções APS.
Este artigo não pretende explorar detalhadamente tais metodologias nem tampouco propor uma nova sistemática de seleção. Entretanto, algumas diretrizes importantes devem ser consideradas no momento da definição dos softwares que farão parte do processo de seleção, da definição dos fornecedores de serviços de implantação destas soluções e no momento da análise de aderência das opções aos processos da empresa. Estas premissas podem ter impacto direto no sucesso do projeto e são assim descritas:
Ø Escolha dos softwares: os softwares que serão avaliados no processo de seleção deverão, sobretudo, dispor das funcionalidades demandadas pela empresa. É importante também que esses sistemas disponham de um suporte local qualificado para prestar um rápido apoio técnico quando necessário. A abrangência da base instalada também é importante para dar maior segurança em relação à aplicabilidade e à incidência de problemas. Pelo caráter analítico que um APS possui, a usabilidade e boa interface são itens que podem contribuir para a sua utilização. Por fim, neste ponto também é fundamental levar em conta a relação custo–benefício do sistema. Os valores entre uma opção e outra podem variar bastante, sobretudo em função de que estas ferramentas possuem características e abordagens distintas para a programação com capacidade finita e, na maioria das vezes, são de propriedade de fornecedores sediados em outros países.
Ø Qualificação dos fornecedores: a escolha do fornecedor adequado para conduzir o projeto de implantação deve levar em conta a existência de uma: (1) equipe qualificada e que tenha amplos conhecimentos em PPCP e engenharia de produção; (2) metodologia de implantação consolidada; (3) suporte pós-implantação; e (4) cases de sucesso e clientes de referência. Uma boa estratégia neste item é realizar visitas técnicas em clientes do fornecedor.
Ø Análise de modelagens e protótipos: o desenvolvimento de protótipos com os produtos e processos da empresa é, sem dúvida, a melhor maneira de avaliar a aderência da ferramenta, a flexibilidade e a qualidade na resposta do fornecedor do APS. As empresas devem modelar um problema de sequenciamento com dados que representem de forma sucinta a sua realidade e enviar estes dados para que os fornecedores elaborem os seus protótipos e façam demonstrações dirigidas para posterior avaliação.
Definir escopo correto e aderente ao negócio da empresa
A implantação de um software APS não segue apenas um modelo convencional de aplicação e integração. Dependendo do tipo de orientação do sistema produtivo (voltado contra pedido ou contra estoque), das características do processo produtivo, dos demais sistemas envolvidos no planejamento e dos objetivos principais que se deseja atingir, o formato da solução pode ser definido de uma forma bastante diferente. É comum observarmos casos de empresas muito semelhantes sob o ponto de vista do negócio e do sistema produtivo, mas com soluções APS bastante distantes, sendo que ambas obtêm resultados expressivos utilizando a sua ferramenta. Isto se deve pela facilidade de adaptação de uma ferramenta APS para necessidades distintas, permitindo focar a modelagem do sistema de acordo com as características do ambiente e aos objetivos específicos que a solução se propõe a atender.
Desta forma, destaca-se a importância de identificar um formato de utilização e integração que esteja alinhado às estratégias da empresa. Neste sentido, muitas vezes sugere-se iniciar o processo com um diagnóstico de prontidão e especificação ou com um projeto piloto limitado a uma área específica da empresa.
Aproveitar os sistemas existentes
Uma importante premissa para um projeto de implantação de um software APS é o aproveitamento máximo dos recursos técnicos já disponíveis na empresa, incluindo sistemas de informação, tecnologia de hardware e interfaces de comunicação. Desta forma, é possível reduzir de forma significativa as despesas, esforços e tempo de implantação. Um exemplo desta situação é verificado nos casos em que a empresa já possui um sistema MRP, mesmo que não esteja atendendo às necessidades de forma plenamente satisfatória, e decide abandoná-lo para realizar a explosão das necessidades e geração de ordens pelo APS.
Na prática, o que se verifica nestes casos é que as mesmas dificuldades que limitaram o uso do MRP no passado são agora transferidas para o APS ou poderiam ser solucionadas de forma razoavelmente simples. Conforme vimos anteriormente, o APS potencializa e, muitas vezes, torna o MRP viável através da atualização das ordens com datas realistas respeitando a capacidade de produção, mas isto pode ser obtido através de uma simples interface de atualização de dados entre os dois sistemas.
Além das desvantagens de desviar o foco do projeto, ampliar as despesas de licenciamento e implantação e realizar uma nova implantação de um módulo existente, é preciso ainda ter cuidado para garantir que não haverá perda ou duplicidade de informações importantes para outros processos no ERP (custos gerenciais, por exemplo). Portanto, é fundamental identificar na fase de elaboração do escopo do projeto quais os sistemas deverão estar integrados para aproveitar, na medida do possível, os investimentos já realizados. Ao atender esta premissa, fica definida de forma clara e objetiva a participação de cada sistema no ciclo de PPCP, explorando as potencialidades e preenchendo as lacunas adequadamente.
Organizar a estrutura de dados
Toda implantação de um sistema demanda uma correta base dados para que o seu funcionamento não seja prejudicado. No caso de um sistema APS, as principais informações necessárias para o desenvolvimento de uma modelagem são: cadastro de produtos, roteiros de produção, tempos de preparação e de operação, estoques, turnos de trabalho e cadastro de máquinas.
Geralmente estes dados que estão cadastrados no ERP precisam passar por uma revisão no momento da implantação. Além disso, é muito importante que seja determinada uma sistemática para garantir a manutenção destas informações, uma vez que novos produtos são desenvolvidos, melhorias nos processos produtivos são realizadas e os tempos de processamento passam por modificações.
Designar equipe qualificada
Para a obtenção de resultados expressivos é preciso contar com uma equipe qualificada e devidamente comprometida e dedicada com o projeto de implantação. As características de um projeto de sistema APS pressupõem a alocação de uma equipe de alta capacitação técnica e multidisciplinar. Assegurando a devida transferência e absorção dos conhecimentos necessários, pode ser garantida uma maior aderência da solução e segurança durante e após o início da utilização do software.
Neste sentido, é fundamental a alocação de um gerente de projeto com disponibilidade, dedicação, poder de decisão e capacidade de exercer efetiva liderança sobre o grupo. A definição de alocação dos envolvidos da área de TI deve garantir que os esforços necessários da área de tecnologia sejam cumpridos de forma efetiva e dinâmica. Da mesma forma, os envolvidos das áreas de suprimentos, vendas e engenharia devem estar devidamente comprometidos e alinhados com os objetivos gerais do projeto para garantir a efetividade das ações necessárias.
Por fim, destaca-se com prioritária relevância, a definição de usuários-chave (key user) com alta capacidade analítica, destreza computacional, facilidade de aprendizado, disponibilidade de dedicação, visão crítica e prospectiva e que tenha conhecimentos do negócio da empresa e de conceitos de engenharia de produção. Este fator é fundamentalmente relevante devido à característica analítica das ferramentas APS, que dependem da capacidade intelectual e técnica do usuário para interagir, avaliar o impacto das decisões e com isto atingir todo o potencial de desempenho que a solução pode proporcionar.
Estabelecer e cumprir a metodologiade implantação
De acordo com o Estudo de Benchmarking em Gerenciamento de Projeto realizado pelo PMI-BR em 2007, apenas 41% dos projetos da área de TI realizados no Brasil conseguem atender plenamente às expectativas dos clientes. Considerando que a implantação de um sistema APS possui o agravante de interferir na cultura da empresa e na relação de poder entre os envolvidos e requer o envolvimento de diversas áreas da empresa de forma sinérgica, podemos constatar que a gestão de projetos é um fator essencial para minimizar os riscos de insucesso.
Portanto, deve-se adotar uma metodologia de implantação formal e consolidada que conte com o apoio de ferramentas colaborativas para estreitar a comunicação entre todos os envolvidos e que contribua para a obtenção dos prazos e metas estipulados. Por fim, deve ser considerado que o impacto da mudança cultural precisa ser absorvido através de uma implementação gradual e que as tarefas e responsabilidades de cada um dos envolvidos devem estar claras e bem definidas.
“Uma estratégia que busca a excelência na gestão da produção como forma de diferenciação não pode estar apoiada em modelos convencionais e sistemas ultrapassados. A decisão estratégica que envolve superação de desafios acelera a maturidade e ajuda a resolver problemas antigos, fazendo a empresa alcançar níveis superiores de competitividade. Atualmente, as empresas de classe mundial estão adotando ferramentas de programação com capacidade finita, superando dificuldades conhecidas e dando um importante passo para alcançar uma vantagem competitiva em relação aos concorrentes.”
Principais tendências no Brasil
Este capítulo tem o objetivo de apresentar algumas tendências de aplicações do APS no Brasil. De forma geral, as análises apresentadas dizem respeito a experiências dos autores através de constatações colhidas no meio acadêmico e empresarial. Estas discussões vêm sendo tratadas em cursos de extensão, eventos de Supply Chain, dissertações de mestrado, aulas de Engenharia de Produção, bem como em projetos de APS vivenciados pelos autores.
Regras personalizadas de otimização
Considerando a sua aptidão para tratar modelagens complexas com múltiplas restrições e a sua flexibilidade para personalizar regras especiais, os softwares APS têm se destacado em aplicações com regras personalizadas para negócios específicos. Uma aplicação típica deste tipo de regra consiste na resolução de problemas complexos de otimização de recursos com características especiais de ocupação de capacidade. Estas soluções geralmente são focadas em minimização do tempo total de setup, maximização da performance de entrega dos pedidos e minimização do estoque em processo. Indústrias de processo contínuo (por exemplo, tanques de preparação e linhas de envase) e sistemas produtivos que possuem recursos que processam múltiplos produtos simultaneamente baseado em suas características (por exemplo, tratamento térmico, rotomoldagem e injetoras rotativas) são os casos mais comuns encontrados nas empresas que utilizam este tipo de tecnologia no Brasil.
Apesar da complexidade envolvida nestes modelos, os cenários destas aplicações envolvem carências importantes para as empresas.
Considerando que as soluções utilizadas na prática pela maioria das empresas geralmente não utilizam a tecnologia apropriada (o mais comum são planilhas eletrônicas) e se baseiam na simplificação do problema para gerar um resultado viável, torna-se evidente que os ganhos oriundos de uma implantação de sistema APS com regra personalizada de otimização tendem a ser ainda mais expressivos do que os ganhos obtidos em aplicações convencionais. Considerando ainda que o aumento crescente dos casos de sucesso de implantação deste tipo de solução incentiva outras empresas e aumenta a experiência dos fornecedores, devemos considerar a utilização de regras personalizadas de otimização como uma forte tendência nas aplicações das soluções APS no Brasil.
Soluções de planejamento com capacidade finita
Considerando a crescente necessidade das empresas em personalizar os seus produtos com base nos requisitos dos clientes visando garantir a competitividade no mercado, cada vez torna-se mais necessária a adoção de políticas de atendimento contra pedido (make-to-order), como forma de reduzir os estoques e viabilizar o aumento da variedade de produtos. Desta forma, a produção baseada em previsão (make-to-stock) tende a ser utilizada principalmente para complementar a ocupação da capacidade produtiva quando a carteira de pedidos não é suficiente para garantir uma boa ocupação dos recursos.
Com base neste cenário, uma condição muito importante para o negócio é o estabelecimento de um plano mestre de produção com um volume e mix que esteja coerente com a real capacidade dos recursos. Caso contrário, a utilização dos recursos produtivos poderá ficar comprometida com a produção direcionada para previsão enquanto pedidos são atrasados (capacidade superestimada) ou ficar ociosa reduzindo os índices de eficiência e produtividade (capacidade subestimada). Conforme apresentado nos capítulos anteriores, o plano mestre gerado pelo MRP ou pelo MRPII está baseado no conceito de capacidade infinita não possuindo todos os recursos tecnológicos que estão disponíveis nos sistemas APS para tratar as restrições dos processos produtivos. Com isso, a utilização das soluções de planejamento com capacidade finita tende a ser ainda mais ampliada e explorada para a determinação de um plano de produção viável e otimizado. Nas soluções de planejamento com os sistemas APS, o objetivo é realizar a programação e simular alterações com base na demanda firme e prevista no intuito de adequar as datas e quantidades do plano mestre de produção antes de efetivá-lo.
Integração entre soluções APS e S&OP
Assim como o APS, as implantações de soluções de S&OP (Sales and Operations Plannig ou Planejamento de Vendas e Operações) têm demonstrado um crescimento significativo de aplicações nas indústrias do Brasil. De maneira geral, o S&OP busca o balanceamento entre capacidade e demanda, alinhando assim os planos estratégicos aos operacionais. Em uma análise de tendências para o mercado de S&OP, Wallace (2004) afirmou que as ferramentas APS podem ser extremamente benéficas para a análise de capacidade e restrições frente aos planos de vendas desenvolvidos no processo de Planejamento de Demanda. Esta visão do autor está bastante alinhada ao que foi apresentado neste artigo.
Conforme foi visto, os sistemas APS trabalham com uma visão de capacidade finita, avaliando restrições de máquinas, pessoas, ferramentas e demais recursos que limitam a disponibilidade da fábrica. Portanto, entende-se que uma resposta confiável para a viabilidade ou não dos planos de vendas gerados pelo S&OP pode ser melhor alcançada com o uso de um software APS.
Aproximação com Lean Manufacturing
Os princípios da produção enxuta (Lean Manufacturing) propõem o ataque às perdas produtivas como forma de tornar a empresa mais competitiva. De acordo com esta teoria, os principais fatores de desperdício são: (1) produção em excesso, (2) estoques em excesso, (3) movimentação desnecessária de pessoas e materiais, (4) tempo de espera acima do necessário e (v) redução de sucata.
Nos últimos anos, uma série de iniciativas têm sido implementadas nas empresas para adotar esta filosofia, sempre com o objetivo comum de entregar os pedidos na data combinada, com mínimo de estoque, menores lead times possíveis e máxima utilização dos recursos. Entretanto, a utilização de ferramentas tecnológicas nos projetos de Lean Manufacturing ainda está em fase inicial de maturidade no Brasil, de forma que as soluções baseadas em um sistema avançado de planejamento geralmente são preteridas por modelos de gestão visual ou programação puxada através de kanban.
Apesar da origem dos sistemas APS estar no passado bastante associada a uma referência que sempre esteve alinhada aos conceitos da produção enxuta, a Teoria das Restrições (TOC), os sistemas APS evoluíram com regras mais flexíveis do que simplesmente subordinar a programação ao gargalo, possibilitando uma maior flexibilidade e facilidade de adaptação a diferentes ambientes. Recentemente, a aproximação entre as empresas Toyota, principal promotor e referência de produção enxuta no mundo, e a Preactor International, empresa que atua na categoria de soluções APS, tem gerado uma série de novas iniciativas para aproximar as técnicas do Lean Manufacturing das soluções de programação com capacidade finita. Além das aplicações convencionais para sincronização, otimização de setup e maximização da performance de entrega, algumas soluções exclusivas para alinhamento com a filosofia Lean estão sendo desenvolvidas, com destaque para a aplicação de cálculo de nivelamento de produção Heijunka de forma automática, otimizada e dinâmica de acordo com a variação no mix da demanda. Estas soluções específicas, associadas aos diversos casos de sucesso de empresas que procuraram se tornar mais enxutas através do uso de uma programação fina eficiente e da tomada de decisões baseada em simulações detalhadas de produção, têm despertado um novo modelo de alinhamento entre os projetos de APS e Lean Manufacturing.
Tecnologia no chão de fábrica
Ao realizar a implantação de um sistema APS, o setor de PCP das empresas tende a absorver maior domínio sobre a produção, gerando planos mais otimizados, abrangentes e detalhados. É comum que cada um dos recursos produtivos receba uma programação detalhada das tarefas a serem realizadas, sendo este plano atualizado sempre que houver alguma mudança significativa na programação. Neste sentido, torna-se ainda mais importante que a distribuição das informações do PCP para o chão de fábrica seja feita de forma bastante eficaz, como forma de garantir que as modificações necessárias na programação sejam devidamente informadas na produção. Além disso, o planejamento fino aumenta significativamente a necessidade de obter feedback sobre aquilo que está sendo produzido e de receber informações dos imprevistos ocorridos, para que as novas condições sejam consideradas no momento de refazer e atualizar a programação para a fábrica novamente.
Para aumentar esta interatividade entre o PCP e a fábrica, cada vez mais soluções tecnológicas para o controle da produção tem sido utilizadas. As listas de tarefas das ordens de produção que devem ser realizadas são transmitidas através de monitores LCD, enquanto quadros Andon divulgam importantes feedbacks sobre o desempenho realizado. A coleta de dados automática, através de terminais ou de sistemas supervisórios, aumenta significativamente a qualidade dos apontamentos, sendo esta mais uma tendência nas empresas que buscam soluções APS.
Utilização em cursos de Engenharia de Produção
Cursos de graduação ou de pós-graduação em engenharia de produção e áreas afins dificilmente possuem um laboratório tradicional para atividades práticas. Na maioria das vezes, o que se verifica nas instituições de ensino é a existência de um laboratório informatizado, sendo este um ambiente ideal para estimular o ensino através de atividades práticas com o uso de softwares.
Assim sendo, a apresentação de workshops práticos com auxilio de recurso computacional para modelar um sistema produtivo em um software APS e a aplicação de exercícios de simulação de cenários demonstram-se como fatores diferenciais para consolidar os conhecimentos teóricos e aproximar os ensinamentos macadêmicos às reais necessidades das empresas.
Aplicações em serviços
Os sistemas baseados nos conceitos de gerenciamento de projetos, que algumas vezes são considerados como principal alternativa para a programação de operações no setor de serviços, devem ser encarados como aplicações baseados em atividades e não em recursos. Por este motivo, geralmente não são indicados para programação quando existem recursos compartilhados por diversas demandas e o foco de otimização está em melhor utilizá-los.
Os sistemas APS, por sua vez, utilizam o conceito de programação com capacidade finita, sendo recomendado para o planejamento das operações do setor de serviços quando existe a preocupação de gerenciar, alocar e controlar a demanda considerando que os recursos são compartilhados por múltiplas tarefas e a capacidade de atendimento é limitada.
Neste sentido, a adoção de modelos de programação com softwares APS baseado em atividades alocadas em recursos humanos mostra-se como uma tendência para as empresas do setor de serviços que buscam racionalizar a sua mão de obra, simular cenários para tomada de decisões, sincronizar os processos e obter um melhor controle sobre as suas atividades.
Considerações finais
Notadamente, a gestão da manufatura é a área que mais carece de sistemas de gestão que realmente atendam às necessidades essenciais do negócio. Mesmo com o amadurecimento e melhor aproveitamento dos sistemas ERP, é muito comum em empresas de todos os portes a utilização de planilhas eletrônicas para suportar a realidade da programação da produção, como forma de realizar de forma manual aquilo que o sistema corporativo não atende. Entretanto, o advento dos softwares APS trouxe a possibilidade de preencher esta importante lacuna, aplicando conceitos de programação da produção com capacidade finita e utilizando alta tecnologia computacional para modelar os sistemas produtivos e gerar planos de produção de forma realista e otimizada.
Este artigo mostrou quais são os principais desafios que devem ser considerados pelas empresas que procuram este tipo de ferramenta e conhecê-los antecipadamente é um fator fundamental para planejar adequadamente ações necessárias para aumentar as chances de sucesso. Além disso, foram destacadas as principais tendências de aplicação destes sistemas no Brasil, ajudando a compreender não apenas como funciona esta tecnologia, mas também de que forma ela vem evoluindo.
Espera-se que esta leitura contribua para as empresas estarem alinhadas às melhores práticas adotadas no mercado no que se refere a implantações de ferramentas de programação com capacidade finita, auxiliando-as assim para a melhor condução de projetos APS. O artigo não teve a pretensão de esgotar aqui os assuntos levantados. Espera-se que novos estudos sejam realizados e que contribuam para a evolução deste tema.
Referências
Ø CARVALHO, D. (2009) – Os softwares que tornam sua empresa mais competitiva. Tecmaran Consultoria.
Ø CORRÊA, H. L; GIANESI, I. G; CAON, M. (2001) – Planejamento, Programação e Controle da Produção. São Paulo: Atlas.
Ø FAÉ, C. S; ERHART, A. A introdução das ferramentas APS nos sistemas de planejamento, programação e controle da produção. Encontro Nacional de Engenharia de Produção. Porto Alegre, 2005.
Ø ERHART, A.; FAÉ, C. S.; MENESES, G. Sistemas Avançados de Planejamento da Produção: Uma Aplicação na Indústria Moveleira. X Simpósio de Administração da Produção, Logística e Operações Internacionais. Rio de Janeiro, 2007.
Ø RITZMAN, L.P. & KRAJEWSKI, L.J. (2004) – Administração da Produção e Operações. São Paulo: Prentice Hall.
Ø TUBINO, D. F. (2007) – Planejamento e Controle da Produção: Teoria e Prática. São Paulo: Editora Atlas.
Ø VOLMANN, T. E; BERRY, W. L; WHYBARK, D. C. (1997) – Manufacturing planning and control systems, 4ª ed. Boston: McGraw-Hill.
Ø WALLACE, T. F. (2004) – Sales and Operations Planning: The “how-to” handbook. T. F. Wallace & Company.
Ø ZATTAR, I.C. (2004) – Análise da aplicação dos Sistemas Baseados no Conceito de Capacidade Finita nos diversos níveis da administração da manufatura através de estudos de caso. Tese de Mestrado. UFSC.
Artigo publicado na edição 10 da revista Mundo Logística – Edição: Maio/ Junho 2009
Autores
Cristhiano Stefani Faé (csfae@accera.com.br): é graduado e mestre em Engenharia de Produção pela UFRGS. Possui grande experiência em projetos APS e como consultor e instrutor atua nas áreas de Gestão de Estoques, Planejamento de Demanda e Gestão Avançada da Produção. Atualmente, é diretor executivo da ACCERA Supply Chain Solutions.
Alexandre Erhart (alexandre@accera.com.br): é engenheiro de Produção pela UFRGS com MBA em Logística Empresarial pela Fundação Getúlio Vargas – FGV. Possui grande experiência de consultoria em gestão avançada da produção e diversos casos de sucesso de implantação de sistemas APS. É certificado PMP pelo Project Management Institute. Atualmente, é diretor de Projetos e responsável pela unidade de negócios de Programação Fina da Produção na ACCERA Supply Chain Solutions